top of page
Siliciumcarbide lepfilmschijf
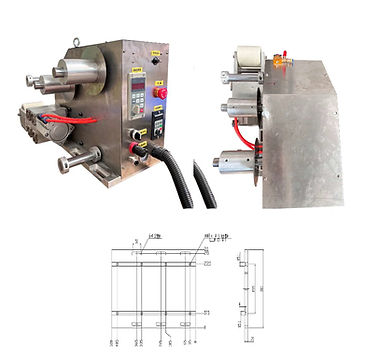
Siliciumdioxide lepfilmschijf bestaat uit een mylar-film bedekt met hars die siliciumdioxidedeeltjes bevat. Het wordt aanbevolen voor eindpolijsttoepassingen waarbij randbehoud belangrijk is. Aanbevolen als alternatief voor colloïden en doeken voor het uiteindelijke polijsten van SEM- en TEM-monsters. Siliciumcarbide- en siliciumdioxide-lepfilms bestaan uit een mylar-film bedekt met hars die siliciumcarbide- of siliciumdioxidedeeltjes bevat. Ze worden aanbevolen voor fijnslijp- en leptoepassingen waarbij randbehoud belangrijk is.
Functies:
* Micron-gegradeerd premium schuurmiddel om nauwkeurige afwerkingen te produceren
* Precisierug voor uniformiteit en vlakheid van het monster
* Bestand tegen water, olie en de meeste oplosmiddelen
* Gebruik voor niet-ingekapselde monsters
* Niet aanbevolen voor toepassingen met powerheads
Diameter: 4" 6" 8"
Montage: PSA (Pad) Ruwheidsgraad:
Mesh _cc781905-5cde-3194-bb37819d05-5bad5cfde-136 -bb3b-136bad5cf58d_ :15000
Deeltjesgrootte/µm: 0,3
Type: SiliciumDioxideLappende filmschijf
-
What material is used for diamond lapping?Boron Carbide It is a preferred abrasive for hard materials. E.g. Tungsten Carbide, tempered steel. Boron carbide abrasive is an extremely aggressive cutting, ultra high stock removal product. It is recommended only for lapping the hardest materials, generally limited to tungsten carbide and titanium carbide.
-
How do you clean a diamond lapping plate?Using your nylon brush, spread the Bar Keepers Friend evenly on the stone. Gently scrub the stone with the nylon brush for a minute or two. Rinse the stone off with warm water while continuing to gently scrub with the brush.
-
How to use diamond lapping film?To use Lapping Films, simply peel a strip off the sheet and stick it to the platen.Center the strip as much as possible. That's it! Unlike Diamond Stones, you'll want to use the edge-trailing stroke (up and away) with Lapping Films.
-
What is the purpose of lapping?Lapping is an averaging process where the greatest material removal occurs where the high points of the surface of the part contact the flat lap plate. The object is to produce parts with a uniformly smooth and usually flat surface.
-
How much material does lapping remove?The lapping process is more gentle than honing and removes much less surface material. Therefore, the workpiece should be as close as possible to final size — achieved, for example, through double-disk grinding — because lapping typically removes only 0.0005” to 0.005” (0.0127 mm to 0.127 mm) of material.
-
What is diamond lapping fluid made of?Diamond lapping fluid, also known as water-soluble coolant, is commonly used in conjunction with diamond lapping films and other precision polishing tools. This type of coolant enhances the water with additional features to improve the lapping process. Here are the details, benefits, and some challenges associated with using Diamond lapping fluid: Benefits of Diamond Fapping Fluid Enhanced Cooling: Diamond lapping fluid improves the cooling efficiency of water, helping to dissipate heat generated during the lapping process. This prevents overheating and potential damage to both the workpiece and the lapping film. Lubrication: The fluid provides better lubrication than plain water, reducing friction between the abrasive film and the workpiece. This helps in achieving a smoother finish and extending the life of the lapping film. Particle Suspension: It helps to suspend the abrasive particles and swarf (material removed from the workpiece) in the coolant, preventing clogging of the lapping film and ensuring a consistent cutting action. Corrosion Protection: Many Diamond lapping fluids contain additives that protect both the workpiece and the lapping equipment from corrosion, especially when working with metals. Challenges of Using Diamond Fapping Fluid Concentration Management: As the water component of the coolant evaporates, the concentration of the fluid increases. This can lead to changes in the performance of the fluid, potentially causing issues with consistency and effectiveness. Regular monitoring and adjustment are necessary to maintain the correct concentration. Frequent Testing: To ensure optimal performance, the concentration of the lapping fluid needs to be tested frequently. This adds an extra maintenance step and requires the use of appropriate testing equipment and methods. Potential Residue: If not managed properly, the evaporation of water can leave behind residues that may affect the lapping process or the final finish of the workpiece. Storage and Handling: Proper storage and handling are required to maintain the efficacy of the Diamond lapping fluid. Contamination or improper storage conditions can degrade the fluid’s performance. Best Practices for Using Diamond Fapping Fluid Regular Monitoring: Implement a regular schedule for testing the concentration of the lapping fluid and adjusting it as necessary. Use a refractometer or other suitable devices to measure concentration accurately. Top-Up with Water: Regularly top up the fluid with water to compensate for evaporation and maintain the appropriate concentration. Clean Work Environment: Ensure that the work environment and all equipment used are kept clean to prevent contamination of the lapping fluid. Proper Storage: Store the fluid in a cool, dry place and keep containers sealed when not in use to prevent contamination and evaporation. By following these best practices, the advantages of using Diamond lapping fluid can be maximized while mitigating the potential challenges associated with its use.
-
What material is best for lapping?Diamond slurries are often used in precision lapping applications, as they offer several advantages over traditional abrasives such as Alumina or silicon carbide. Diamond particles are harder and more durable than these traditional abrasives, allowing for faster material removal and improved surface finish.
-
Is aluminum oxide better than diamond lapping film?When comparing aluminum oxide to Diamond lapping film for precision polishing, diamond lapping film is generally considered superior. Here are the key reasons why Diamond lapping film is better than aluminum oxide: Superior Hardness: Diamond is the hardest known material, significantly harder than aluminum oxide . This allows Diamond lapping film to cut through materials more efficiently and maintain its cutting ability over a longer period. Higher Cutting Performance: The superior hardness of Diamond translates to higher cutting performance. Diamond particles can cut and abrade materials more quickly and effectively than aluminum oxide , which results in faster material removal rates and more efficient polishing processes. Durability: Diamond lapping film is more durable due to the inherent toughness of Diamond particles. This means the abrasive surface remains effective for a longer period, reducing the need for frequent replacements and thus offering better cost-effectiveness over time. Precision and Consistency: Diamond lapping film provides a more consistent and precise finish. The uniformity of Diamond particles and their ability to maintain sharpness ensures a uniform surface finish, which is crucial in high-precision applications. Versatility: Diamond lapping film can be used on a wider range of materials, including very hard substrates such as ceramics, carbide, and hardened steels. aluminum oxide, while effective, may not perform as well on these tougher materials. Reduction in Surface Damage: The cutting efficiency and sharpness of Diamond particles help in reducing the heat generated during the lapping process, which minimizes the risk of surface damage such as burns or cracks. In summary, Diamond lapping film offers better performance, durability, and precision compared to aluminum oxide, making it the preferred choice for high-precision and demanding polishing tasks.
-
What is the process of diamond lapping?Diamond lapping is a material removal method using fixed diamond abrasive particles which produce long chips of the component material. The process of making chips with a sharp abrasive grain produces the lowest amount of deformation in the component while giving the highest removal rate.
bottom of page